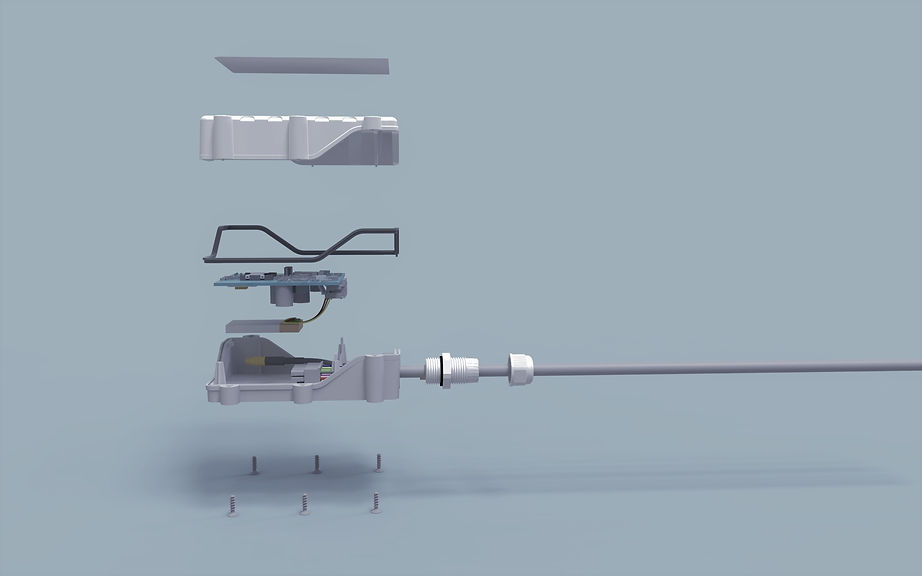
Injection Molding Prototyping
Prototyping refers to an experiment wherein organizations tend to implement ideas from a piece of paper to computerization and then make a physical, tangible product. With prototypes, plans can get improved and authenticated so that the company delivers desirable and accurate products.
Table of Contents:
​
Introduction to Injection Molding Prototyping
​
Prototyping remains the first step in figuring out hidden obstructions and unanticipated challenges as well as the underlying feel and looks of the product, leading to minimized product failure chances—the product that is likely to be achieved at the end of the manufacturing process. Prototyping ensures eliminating potential quality control issues and helps manufacturers analyze the final product on-ground realities. Furthermore, it has diverse applications that add massive value to the manufacturing process. For example:
-
Helps testing various plastic materials
-
Confirms if the geometry of the part is feasible or not
-
Makes sure the durability of product by stress analysis
-
Presents a physical model of the final product which is likely to be produced
​
When is Prototyping needed?
Prototyping has now become an essential part of injection molding practices. The mainstreaming of prototyping is to ensure the quality of the product and analyze it under certain circumstances, likely to act on the final product under daily use. At the same time, the concept of prototyping is encouraged for low-volume production. Without a doubt, low-volume production is required either when a new development is being done or when complex and very high-quality parts (micro-injection molding) are needed. In both cases, prototyping is a natural product development phase required across all industries and manufacturing processes.
In the first case, prototypes serve various purposes that include:
-
Justifying the product idea to potential financial backers and investors.
-
Provoking feedback from likely customers.
-
Analyzing functionality and the injection molding process feasibility.
In the second case, injection molding of micro parts is a sensitive and precision-demanding operation that is difficult to meet without a prototype wherein the components get analyzed under operational conditions. The prototyping of the final part usually reveals if the design could get more optimized or not. The tolerance levels of prototyped parts are analyzed, and the design and features such as material, molding temperature, and demolding pressure are also checked.
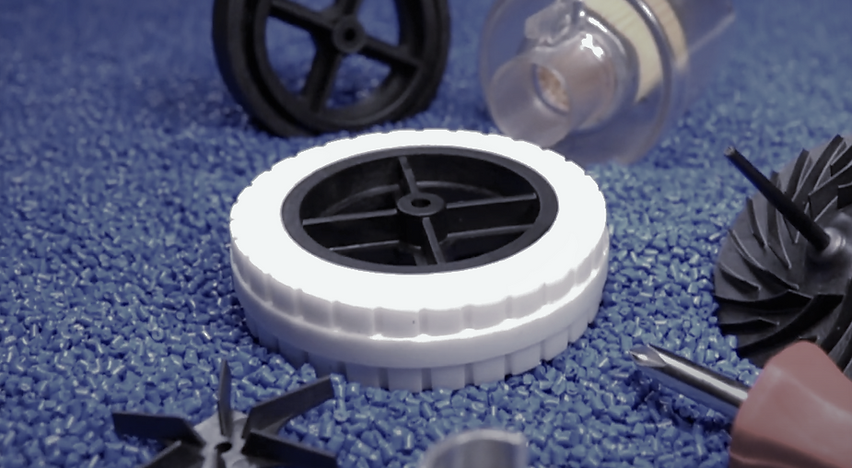
Why is Prototyping key in Injection Molding?
Whatever the product a company is intended to produce, a prototype is necessary for the design process and better quality. That is how engineers and mold makers will be on the top to avoid any design and other manufacturing processes complexities. Along these lines, here are some reasons why prototyping is critical in injection molding:
1. Testing and Evaluating the Design
Unluckily, designs, drawings, and ideas are sometimes a far cry away from the real world where the product is to be used. But with the help of creating a prototype, it becomes possible to check and analyze the product on a factual basis. An accurate product model helps to understand which part of the product is worthwhile and which one needs to be revised. Similarly, it is equally possible to receive omissions that were not noticeable on the piece of paper. Besides its evaluation, the team of experts and designers find an ample opportunity to test the product under a specific environment that inflicts stresses on the original part in its serving tenure.

​
2. Clarifying Issues and Production Costs
Prototypes can appropriately characterize the shape, size, and function of a part. They can also prompt more meaningful and effective communication between design and manufacturing departments, facilitating a durable and efficient product. Furthermore, the whole production process becomes apparent, and then it could be checked on the reality grounds if any of the operations could get optimized, improved, or even removed. It will streamline the production and bring about minimizing costs in the overall production cycle.
3. Grasping the Marketing Opportunities
Unless there is a physical model of the product, it will not be possible to attain the opportunities in the market associated with that specific product. Without a prototype or physical representation of the product, it is impossible to get potential clients and make them commit to purchase the product. But with the help of the product in hand, the concept instantly converts into reality, and it is easier to crack a purchasing deal at that moment.
4. Increasing Brand Confidence and Trust
Without prototyping, a completed project may induce questions because of the lack of information about the project and its inability to convey the promised idea. However, prototyping fills up that gap before implementation. It enables the brand to develop personal relationships with financial backers and buyers, making it effortless to measure a project's growth and foster credibility.
5. Getting Patents Registered
If the product is unique and new, patents must be considered. There are massive chances for copying a product's design that adds undue competition for original manufacturers with such a product. Subsequently, with the help of a prototype in hand, it is best to sit with the patent attorney and get the patents of the design registered in the company's name.
How to do Prototyping?
The following are the three steps streamlined to make a prototype of a part or a product:
1. Creation of a Plastic Product Design
The fundamental step of manufacturing always belongs to design. Whatever product is to be manufactured, its design is the first and foremost step towards the actual part. While making the design for a plastic part, keep a realistic approach and see if the design concept is practical or not. But remember, not all designs can be manufactured with injection molding. Consequently, there is a need to team up with plastic specialists and perform design optimization for injection molding technology and then 3D prototyping to ensure the engineering-for-production of that design. Likewise, ideas can be designed, or even animated videos can be created to give a realistic view of the intentional product from multiple aspects.
2. Engineering of a Product
Product engineering of the design is typically related to maintaining the technical aspects decided in the design. For example, design entails a specific thickness for the final product, so the thickness of the prototype should also be an exact match of the decided plan. For this purpose, an analysis of design is mandatory to know whether it will be feasible with this thickness or not.
3. Prototyping with Injection Molding
Prototype injection molding includes the utilization of plates that will push the mold's one part, and water lines are streamed for the cooling cycle once the cavities are loaded up with the injected material. Whether it is a small and straightforward or complex prototype, mold can be created for prototyping. It is essential to know that if the prototype is complex, mold should be made using special resins to achieve high levels of accuracy. On the other hand, in small and straightforward prototypes, cheap aluminum molds and rapid tooling should be considered—moreover, the smaller the molding machine, the lower the cost.
Furthermore, prototyping assists to decide among the types of molds. 3D printed models visualize both single-cavity and multi cavity molds, and this makes it easier to choose the right type for a specific project.
Once the making of mold gets done, the following process is carried out using an injection molding machine. A clamp puts together two halves of the mold through extreme hydraulics pressure in injection molding, and then molten material is injected into it. Once it gets cooled solidified, and de-molded, the plastic design has become manifested and taken shape.

Conclusion
The prototype follows the same procedure and protocols followed by the product in its mass-level production. Nevertheless, the only difference is that the former is streamlined to ensure its quality, and the latter operates based on results generated by prototyping.
The potential benefits of prototyping associated with injection molding cannot be overlooked in the interim. It offers cost estimation, design testing & evaluation, smoothness of workflow, minimum errors, marketing opportunities, and improved brand confidence and trust. Moreover, the steps of prototyping have also been discussed above.
Table of Contents:
​
Explore our services:
​
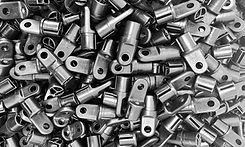