
Injection Molding Dilemmas: Hot or Cold Runners?
A runner refers to a channel cut into the mold that helps the molten plastic flow from the nozzle to the cavity. In injection molding, the runner plays a significant role since it directly influences mold pressure filling, melting temperature, shrinkage of the material, and wrapping of residual stresses. Based on these reasons, the selection of a runner becomes a considerable portion of the process. Meanwhile, runners can get divided into different types based on their shapes. Usually, the runner's shape is parabolic, trapezoid, half-round, wide trapezoid, and quarter-round.
Table of Contents:
​
1. Hot Runner Systems:
​2. Cold Runner Systems:
3.Hot or Cold Runner: How to Make a Choice?
4. Conclusion
Hot Runner Systems
A hot runner system comprises two plates heated with a manifold system to maintain a consistent temperature used to inject the molten material into the mold cavities. There are several categories of hot runner systems, falling into two major categories: internally heated (suitable for better flow control) and externally heated (ideal for thermal-sensitive polymers) runner systems.
Where and When is Hot Runner System Applicable?
The most significant hot runner system applications are found in the plastic injection molding industry, directly or indirectly, related to the automobile industry (interior designing), aviation industry, toy industry, and medical and healthcare industry. Used by mold manufacturers in the United States, Chine, and countries in Europe, the hot runner system could create a manufacturing process cycle that has enhanced overall production quality and shortened manufacturing time.
The hot runner system is used only when mass production with high quality is required; it is expensive, and waste reduction is significant since there is no sprues' and runners' waste. Besides offering a shorter cycle time, it also provides balanced melt flow and easy to initiate mechanism. Alongside, it gives fewer sink marks and under-filled parts when plastic flows through it.
Conditions and Equipment Needed
As far as conditions for hot runner systems are concerned, the runner's temperature and pressure should get noted and maintained. And here are the equipment or parts needed for the hot runner:
-
Inlet: During the molding process, the resin enters the injection molding process through the inlet.
​
-
Manifold: Molten resin enters the heated nozzle to get injected into the mold cavity while passing through the manifold.
​
-
Nozzles: Hot-runner nozzles act as the connection to the cavity. They are designed individually for every new project, which may drive the cost up enormously. Likewise, they either gate into a sub-runner that will prompt the cavity or directly into the part.
​
-
Hot Runners: Hot runners transfer liquid plastic from nozzles into the mold cavities.
​
-
Locating Ring: It refers to the ring whose adjustment gets decided considering the placement of injection mold. Furthermore, it is also responsible for aligning all the nozzles together.
​
-
Heater Technology: Heater technology is described as a hot runner system as-a-whole. Each runner possesses the ability to manage temperature and heating systems to ensure the best performance and cost.
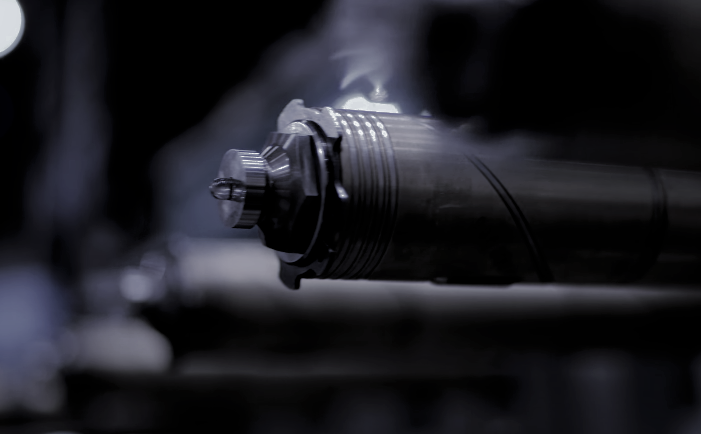
Cold Runner Systems
Cold runner comprises two or three plates present in the base of the mold. The molten raw material is injected into the mold from a nozzle through the sprue, filling the runners' network. Later, this network of runners leads the molten material to the cavities of the mold. Unlike hot runners, cold runners are unheated and disseminate the liquid plastic to the individual mold cavities.
Where and When is Cold Runner System Applicable?
Usually, the final product can be achieved using both the cold and hot runner systems. Still, it might not be economical or suitable to replace a hot runner with a cold runner or a cold runner with a hot runner system. For example, the cold runner is more cost-effective than the hot runner system, but the leading time is higher to have the final product.
Similarly, the cold runner is the most suitable approach for design options and flexible gate location. While adding to its benefits, the cold runner system experiences lower thermal variations because they do not require controllers, heaters, and thermocouples to control the process.
Conditions and Equipment Needed
The cold runner system is a suitable choice for the low production of products. However, the condition depends on the circumstances like raw material, design of the product, and quality required. Talking about equipment or parts of the cold runner system, typically, it comprises of the following three components:
1. Sprue: It is a channel that allows the molten material to enter the mold. Sprue bushing is where the mold's nozzle itself injects the molten plastic towards the cavity.
2. Cold Runner: It refers to an unheated channel that allows the molten material from the sprue to the cavity gate. The cold runner also cools the different segments of the mold system, such as the sprue, gate, and the molded part itself.
3. Gate: Gate is a narrow and small intersection between the mold cavity and the main runner. The gate is the point from where molten material enters the cavity. There are also trimming, chilling/cooling, and metering blenders to control different parameters in a cold runner system.
4. Plates: Within this cold runner system, two or three plates are controlled inside the mold. The two-plate system is simpler to utilize, requiring an injection system to eliminate the part from the mold. In the case of a three-plate system, the runner operates on a separate plate that can be ejected independently from the runner.
​
​

Hot or Cold Runner: How to Make a Choice?
Both hot and cold runners are suitable, however, the demand should get considered. For example, if manufacturers want to reduce the lead time while ensuring a reasonable quality, a hot runner comes up with the best choice. On the other hand, if the lead time is not a problem and manufacturers require extreme quality, it is better to adopt a cold runner system.
Correspondingly, if the capital investment is low, the cold runner is the option because otherwise, the hot runner is expensive. Furthermore, cold runners are a perfect option for low production volumes, such as in prototyping. Conversely, hot runners will, in general, be more financially savvy for medium to high production volumes.
​
Hot Runners Advantages over Cold Runners
Hot runner systems have many benefits over cold runner systems, including:
1. Shorter Cycle Time
Cycle time is a crucial excelling point for hot runners compared with the cold runner system. The wall thickness of the part or runner drives its cooling time. Even optimized cold runners possess 50% to 100% more cycle time than hot runners. Consequently, hot runners can improve the production rate due to the reduced cycle time.
2. Improved Efficiency of the Molding System
A hot runner mold is simpler to start since there are not any hardened or solidified runners to be taken out after each under-filled shot. The mold is all set to function when the operating temperature is reached. Additionally, lower injection pressures can get used, reducing the mold/platen deflection, and minimizing the flash triggered by the movement of mold components.
3. Less Wasted Energy and Material
The waste in the hot runner system is much lower than in the cold runner system. Depending upon the product's design, the cold runner might be equal to 50% to 250% of the mold part weight with a minor regrinding facility of 15%. Other than that, regrinding is an additional step that can reduce the material's mechanical properties and increase energy consumption in cold runners.
Cold Runners Advantages over Hot Runners
The cold runner system also has its benefits associated with the process. Here are some advantages of the cold runner system in comparison to the hot runner system.
1. Useable with Wide Variety of Polymers
Hot runner systems are usually vulnerable to work with a variety of polymers. In contrast, cold runner systems have an excelling edge to this point. Heat-sensitive polymers are very hard to deal with if used in the hot runner system, and most probably, the product falls off its shape. With cold runners, heat-sensitive polymers and polymers of various chemical properties are convenient to use.
2. Inexpensive to Maintain and Produce
Compared with the equipment cost required for the hot runner system, the cold runner system has a clear edge over this point. Due to inexpensive parts and equipment, the overall expenses for these runners are meager. Additionally, maintenance costs are also low since the rates of components or equipment are reasonable, and there is no need to deal with temperature variations.
3. Simplistic Design
Technically, the hot runner system is more complex and challenging to understand than the cold runner system. The components of cold runner systems are straightforward in their designs, so it is easy to work with cold runner systems instead of working with hot runner systems.

Conclusion
Plastic injection molding is a leading force to take the global economies to their culmination. Hardly, there is an industry that does not include the use of plastic injection molding. At the same time, plastic is mandatory, whether it is the health care sector, mass transit projects, aviation industries, toy manufacturing factories, or the automobile industry.
However, plastic injection molding is an intricate process that involves both the hot and cold runner systems. Concerning their use, hot runner systems have more incredible and attractive benefits than cold runner systems. But in some cases, cold runner systems seem, by all accounts, to be the only solution to the problem. In short, both approaches have their importance in their respective fields, and it now depends on requirements if the hot runner is suitable or cold is a better option.
Table of Contents:
​
1. Hot Runner Systems:
​2. Cold Runner Systems:
3.Hot or Cold Runner: How to Make a Choice?
4. Conclusion
Explore our services:
​
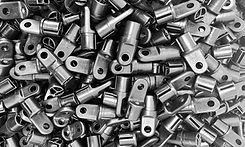