
Design for Manufacturing for Injection Molding
Design for manufacturing or manufacturability (DFM) refers to a process that optimizes the design of a component, part, or product to make it less difficult to manufacture, cheaper, and more convenient to deal with. Typically, design for manufacturing encounters the early stages, most probably, when the process is in the designing phase. At that time, it is easier to optimize the product and reduce unnecessary steps and costs. Ideally, the process of DFM involves these given steps:
-
Easier assembly in later stages: Simplification of product design with the reduction in the number of parts and operations.
-
Technological parts: Designing parts that are easy to manufacture for different technology.
-
Avoiding tight tolerance and designing the product, considering capabilities of the technology available.
-
Effective utilization of available resources.
-
Mistake-proof assembly and product design (Poka-Yoke – a lean manufacturing technique preventing defects and errors in the first place of any process).
-
Incorporation of efficient and easy fastening methods.
Why is DFM Relevant for Injection Molding?
​
DFM combines the engineering and production department in the designing phase, where each ensures maximum utilization of time, cost-effectiveness, quality, and customer satisfaction. Its importance can be gauged from the fact that design decisions control around 70% of a product's manufacturing expenses (materials, processing/handling, and assembly).
​
Meanwhile, in an injection molding process, the successful execution of design for manufacturing is more technical and requires understanding complex applications. The DFM process in injection molding is directly related to an experienced molder. Hence, a deep understanding of the DFM process in injection molding helps for efficient design decisions and offers the benefits of:
​
1. Elimination of Risks
​
In injection molding, streamlining the design for manufacturability can timely figure out and eliminate the potential problems before the product enters the manufacturing process on the mass level. The proper implementation of DFM identifies manufacturability issues while a product is still under designing process. That is how any considerable problem is pre-apprehended, reducing the risks associated with new product development.
​
2. Actionable Recommendations
​
Design for manufacturability possesses an excelling edge over conventional optimization processes since it includes giving actionable recommendations. Highlighting the major manufacturing issues, DFM offers suggestions that are sure to eliminate problems from manufacturing processes. In some cases, minor changes in design can bring the issue down.
​
3. Opportunities to Lowering Costs
​
Design for manufacturing operates as a SWOT Analysis for the injection molding process that figures out strengths, weaknesses, opportunities, and threats of the process. Furthermore, the most valuable feature of this optimization process is its ability to uncover opportunities to lower costs without bringing any considerable changes to the design – form, fit, and function.
​
4. Shorter Product Development Time
​
Primarily, the companies who prepare the design and outsource manufacturing remain a colossal benefit because the design for manufacturing analysis can shorten the product's development time. Consequently, instead of visiting vendors or suppliers for quotes/feedback, engineers can better predict costs and timelines and analyze manufacturability by themselves.
​

Time and Costs Related to DFM
​
DFM is specialized in cutting costs and reducing product development time:
​
How DFM Affects Cost:
​
DFM is highly reliable since it can achieve cost reduction in many ways, and the common of which is reducing the amount of complexity of necessary steps in the process. If operations are minimizable with minor changes in design, time and cost savings are faster to achieve.
​
For example, injection molding plastics are vulnerable to breakage and failure if ejected on shear from the mold. Nevertheless, adding pins for ejection in a strategic location can save on materials' costs. In short, DFM also proves that increasing quality does not have to be always expansive.
​
Let us consider another example. Quite possibly, the most prominent approach to decrease costs is to reduce changes required after tool building. No business wants to suffer the cost brought about by retooling. Given that, design for manufacturing analysis provides injection molding engineers with project insights and intuitions to help them streamline tooling and decrease costs.
​
Moreover, DFM analysis recognizes likely problem areas, design modification opportunities, unsatisfactory draft angles and tolerances, unmachinable features, incomprehensible geometries, calculations, etc. All these actions ultimately point towards cost reduction.
​
How DFM Affects Time:
​
Like reducing costs of processes with mainstreaming DFM, the time for product development also reduces significantly. First, DFM provides engineers with an opportunity to analyze the whole process, and later, this analysis saves much time that might have consumed visiting vendors. At the same time, reducing the total number of operations and standardization of parts and components are also instrumental in reducing the time to the development of the final product. Remember, the standardization of parts refers to a process that expects to take out all the intentional, unintentional, and superficial differences in producing similar and comparable parts to accomplish a critical reduction in the supplier and part production.
How to Optimize DFM – Tips and Tricks
​
1. Adjust with Minimum Number of Parts
​
Reduction in the number of parts directly puts a cut to the investment or cost. Inarguably, fewer parts imply fewer purchases, reduced handling of products, reduced complexity of assembly, and less time for production, engineering, and development, which are considerable benefits in terms of cost and time. Most of the time, the minimum number of parts requires the standardization of the process. For example, parts that do not have relative motion get not made up of different materials. Otherwise, it would make the assembly or parts' service tremendously problematic or impossible. A few ways to deal with part-count reduction depend on using one-piece configurations and selecting manufacturing processes like injection molding.
​
2. Development of Modular Design
​
Simplification of manufacturing activities is directly related to the better implementation of design for manufacturing. Typically, using modular product design approach (subdividing a product into smaller parts in view of their performance, functions, and specifications) simplifies manufacturing activities like testing, assembly, redesign, inspection, purchasing, maintenance, and service expected. The reason is that modules make product updates more flexible in the redesign process, support testing before final assembly, and use standard components to reduce product variations.
​
3. Wise Material Selection
​
The optimum combination between cost-effective material and fabrication directly impacts the manufacturing costs. Even a suitable material supports ease of fabrication, which also means eliminating unnecessary steps like surface finishing, excessive tolerance, and other final operations like polishing/painting that add to the price of the process.
​
4. Minimization of Assembly's Direction
​
Assembly direction plays a vital role in reducing time and cost. Therefore, while adding parts to the assembly, it is suggested to assemble parts from one direction and add them in the standing order from the above side. Later, pieces will attach instantly under the action of gravitational force. What is more, Poka Yoke is a lean manufacturing technique that can be used for mistake-proof assembly. Poka-Yoke is significant to the assemblies and essentially controlled inside the whole production process. Therefore, mistake-proofing methods get used to avoid errors caused by operators. The techniques may include utilizing proximity sensors, vision systems, specially designed fixtures, pins, barcode reader, pressure sensors, warning lights, and speck checking.

5. Minimization of Handling
​
At the same time, handling gets usually used to maintain objects during the processes; however, in DFM, handling also considers positioning, fixing, and orientation of the parts or components. For instance, symmetrical parts must be preferred whenever probable. Otherwise, the asymmetry needs to be amplified to keep away from failures. Besides that, during the designing phase, try to reduce the flow of waste materials or parts in the manufacturing process.
​
Conclusion
​
Design for manufacturing is one of the widely adopted methods that reduce product development time, costs and eliminates all major and potential issues that might be problematic in product mass production. Like other manufacturing processes, DFM is well-known for injection molding as well. In an economic downturn, industries probably implement DFM to achieve high gains with the lowest investment. At the end of the process, DFM saves around 20 to 30% of the costs.
Explore our services:
​
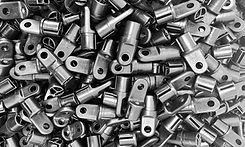